Multi-Parameter Analyser – CRONOS® and CRIUS®

Multi-Parameter Analysers – CRONOS® and CRIUS®4.0
Multi-sensor, multi-channel, multi-parameter analysers can greatly reduce the cost per point of any measurand including pH, residual chlorine, ORP, ozone, chlorine dioxide, dissolved oxygen and turbidity measurements without sacrificing the quality of those measurements.
The CRONOS® and CRIUS®4.0 controllers both allow the connection of multiple sensors. For example, a CRIUS®4.0 may be made up of multi-sensors of the same variety such as up to four chlorine sensors, or could be made up of a mix (multi-channel analyser), such as a pH sensor, a chlorine sensor, and a turbidity sensor. Whatever your requirement for a multi-channel analyser, the CRONOS® and CRIUS®4.0 ranges will provide what you need.
The CRONOS® is a high quality, low cost transmitter designed to give water treatment engineers everything that they need from a transmitter and nothing that they don’t. With no frills, costs can be kept to a minimum whilst optional communications packages allow Profibus, Modbus ASCII, Modbus RTU, Modbus TCP, 4-20mA analogue outputs, and relays for alarms and control.
The CRONOS® has the capability to control up to two sensors of any type with appropriate analogue outputs and relays. Equipped with optional PID control, the CRONOS® is very able to control complex water treatment processes at a fraction of the cost of other controllers.
The CRONOS® can also come in a multitude of languages making it suitable for use in any market.
Customers requiring additional functionality such as downloadable data logging or remote access via the internet should consider the CRIUS®4.0 controller.
The CRIUS®4.0 offers more sensor connections, more functionality and more flexibility with a colour screen and optional built in 3G/4G modem. The CRIUS®4.0 is an attractively priced, top of the range instrument controller. Optional communications packages allow Profibus, Modbus ASCII, Modbus RTU, Modbus TCP and others.
The CRIUS®4.0 is equipped with the capability to connect up to four sensors of any type with appropriate analogue outputs and relays. Four sensors not enough? Simply connect up to 4 CRIUS®4.0 together all using the same display and communications. Equipped with data logging as standard and multiple PID loops as options, the CRIUS®4.0 is very able to control complex water treatment processes at a fraction of the cost of other controllers.
The CRIUS®4.0 can also come in a multitude of languages making it suitable for use in any market.
Customers requiring a no-frills controller should consider the CRONOS® controller.
Water 4.0 and Industry 4.0 Controllers
The phrases ‘Water 4.0’, ‘Industry 4.0’, ‘Internet of Things’ and ‘SMART and DIGITAL’ are now commonly heard but what do they mean and where does Pi fit in? Industry 4.0 relates to the concept that we are living through a 4th Industrial Revolution where factories will be as SMART as they can be. The main principles are based on:
- Interoperability
- Information Transparency
- Technical Assistance
- Decentralisation
Water 4.0 is how this technology and philosophy will be implemented/will affect the water industry. The Internet of Things refers to all devices we use all the time talking to each other and making their own decisions.
It is generally accepted that SMART refers to the increasing sophistication of equipment to make decentralised decisions, so it is this technology that allows for the implementation of Industry 4.0 or Water 4.0, and DIGITAL refers to its comms capability. For example, in 1990 a chlorine analyser measured chlorine in water, gave out a 4-20mA output proportional to the chlorine and a couple of relays.
In 2018 the CRIUS® HaloSense (fully Water 4.0 developed) can provide the 4-20mA output and relays, but also has multiple digital comms options (interoperability), has space for up to 16 sensors (information transparency), has wireless and wired internet access (technical assistance) and full PID capability with remote setpoint, i.e. another device can set the setpoint (decentralisation).
CRONOS®
The CRONOS® is a very capable analyser and controller and includes:
- Up to 2 sensor inputs – the CRONOS® works with all of Pi’s sensors and many more.
- 8 relay outputs – for alarms and process control.
- Process control – via extremely capable PID loops.
CRIUS®4.0
The CRIUS®4.0 controller provides users with numerous benefits:
- Multi-Sensor – reduces costs.
- Onbpard PID and other controls – reduces cost and improves process control.
- Onboard data logging.
- Remote Access via MQTT – live results anywhere in the world.
- Industry leading autocleaning options for sensors – reduced maintenance and cost of ownership.
Summary of Applications
- Water Treatment
- Drinking Water
- Wastewater
- Industrial Water
- Food and Drink
- Pool and Spa Control
- Paper and Pulp
CRONOS®
The CRONOS® is often used in applications where the remote access capability of the CRIUS®4.0 is not required. This doesn’t mean that a CRONOS® doesn’t have the capability of control!
The CRONOS® is a universal controller capable of outputting a PID control signal via an analogue (4-20mA) or a pulse width modulated relay (to control for example, an on/off pump). With the latest in communication options the CRONOS® is capable of running Profibus, Modbus or TCP/IP via Ethernet.
The ability to provide maintenance reminders is very attractive to larger users with multiple operators where it can be easy to miss scheduled maintenance.
CRIUS®4.0
The CRIUS®4.0 is currently used in a multitude of applications and the remote access capability is bringing solutions to our customers’ water treatment requirements.
The CRIUS®4.0 is preferred in the Swimming Pools market, where the superior control and sensor capability provides for better quality bathing water. Again the remote access is proving essential to our customers along with the Variable Speed Drive (VSD) control which is massively reducing electricity usage and CO2 emissions (and reduces the electric bills!).
In the municipal drinking water market, the superior control capability is making it the controller of choice for areas like coagulation control with the superior sensors in use particularly for chlorine control and dissolved oxygen control.
In the industrial market the self cleaning options allow the CRIUS®4.0 to be used for applications that weren’t previously accesible such as in vegetable washing, paper and pulp and meat processing applications.
A CRONOS® or CRIUS®4.0 plus Sensor equals…
- Free Chlorine Analyser (HaloSense)
- Total Chlorine Monitor (HaloSense)
- Chlorine Dioxide Analyser (DioSense)
- Ozone Monitor (OzoSense)
- Dissolved Oxygen Meter (OxySense)
- Suspended Solids Monitor (SoliSense®)
- Turbidity Meter (TurbSense®)
- Streaming Current Monitor (StreamerSense)
- pH Analyser (pHSense)
- ORP Analyser (ORPSense)
- Organics Monitor (UV254Sense)
- Online Conductivity Monitor (ConductiSense)
- Particle Counter (CounterSense)
- Pool and Spa Controller (AquaSense)
- Filter Monitor (FilterSense)
- Fluoride Monitor (FluoriSense)
- External inputs
- Choose from Standard Configurations or ‘Build Your Own’
CRONOS®
The CRONOS® from Pi is an extremely capable, yet low cost controller. It’s only limitations are that it is not capable of remote access (that requires a CRIUS®4.0), and it is restricted to 2 sensor inputs. Options available are:
- Colour display
- Datalogging
CRIUS®4.0
- Remote access via Modem or LAN
- Modbus RS485 or TCP/IP
- Profibus
- PID loops
- Expandable to 32 analogue I/O and 32 digital inputs and 32 relay outputs
- up to 4 sensor inputs expandable to 16
A water quality analyser is a device that allows users (engineers, operators, lab technicians) to measure, control and monitor various parameter throughout their water based applications.
A water quality analyser can be connected to various sensors measuring the same or different parameters around your application. This data can then be sent to another device (i.e. PLC, DCS, HMI), control other devices (using its onboard PID controls) like solenoid valves, dump valves and pumps using analogue or relay outputs, and trigger high and low alarms.
The CRIUS®4.0 is a modular analyser that is capable of being customised to the user’s needs. This saves cost and removes unnecessary programming from the analyser allowing for a better user experience.
If cost is an issue, you don’t need remote access and you have two or less sensors then CRONOS® is the perfect choice.
Water quality analysers are normally installed next to the sensor(s) sample point, although with the CRIUS®4.0 analyser you can install the analyser further away from the sensor(s). The CRIUS®4.0 also has various remote communication options allowing you to send the data from the analyser directly to a device like a PLC which would allow you to remotely view/control the analyser.
The CRIUS®4.0 has sophisticated datalogging which allows the datalogging of all parameters on variable periods. The datalogs can be viewed on the CRIUS®4.0 and also downloaded from the analyser and remotely.
Datalogging is not included on the CRONOS® but is available as an option for an additional cost.
Some water quality analysers have a remote access option that will allow you to connect to the analyser via the internet, or Modbus, and make changes to the process such as adjusting setpoints and open/closing valves.
The CRIUS®4.0 can be communicated to via either Modbus or using Control InSite, Process Instruments remote access.
If a user wants to add additional sensors, outputs or control options to the CRIUS®4.0, they can do this in the field thanks to the modular design of the CRIUS®4.0. The customer would need to contact Process Instruments to purchase the necessary hardware and/or software required and the customer can then install the hardware/software easily by inserting the hardware into the CRIUS®4.0, by loading the software manually or via a µSD card.
Users can easily upgrade the firmware of the CRIUS®4.0 to add additional features that may have been released since the user installed the unit. To do this, the user would simply contact Process Instruments providing their analyser’s serial number. The Process Instruments’ contact would then provide the upgrade file. The upgrade file is then copied to a µSD card and loaded onto the analyser.
The CRONOS® and CRIUS®4.0 allows users to create up to 20 different user accounts. Each account has its own unique password (set by the user) and customisable permissions.
Each user account can be customised to access specific software sections with specific permissions. This allows users to setup certain people with certain access (i.e. a maintenance engineer may need to edit more settings than an everyday operator), and keep users from accessing parts of the analyser they don’t need access to.
The CRIUS®4.0 can record all of its parameters (sensors/controls) into a customisable data log. The data log interval (how often a data point is stored) can be as low as 1 minute and as high as 1 hour. The data logs can be viewed on a graph on the CRIUS®4.0 and displayed on the homepage.
The data logs can be downloaded directly to a µSD card in .csv format, allowing you to quickly open the data in most spreadsheet programs (i.e. Microsoft Excel, LibreOffice Calc, OpenOffice Calc).
The CRIUS®4.0 can store up to 1 million data points. If more storage is required then the user can leave a µSD card in the CRIUS®4.0 and the data will automatically be transferred over to the card every day at midnight. Once the data storage is full, the CRIUS®4.0 will overwrite the oldest data log with the new log.
Focus Ons are a series of short articles distributed by email providing technical information regarding instrumentation, process measurement in potable, waste, process and pool waters. If you would like to join the mailing list, please contact us.
You probably know that Process Instruments offers a cloud based remote access service for our CRIUS®4.0 analyser, but did you know that…
…nearly everything you can do in front of the analyser you can do remotely?
…the CRIUS®4.0 is the first analyser in the world to utilise MQTT, allowing for real time data without a delay?
…customers have seen the number of engineer callouts drastically reduce, saving them time and money?
…Control InSite has been allowing engineers to access CRIUS®4.0 remotely, keeping them safe during COVID?
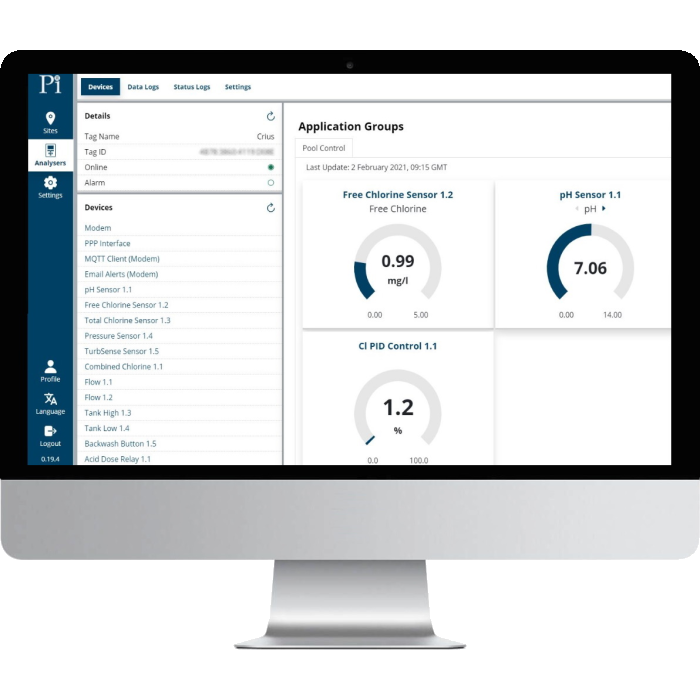
Pi’s sleek and modern remote access solution Control InSite now utilises MQTT (an Internet of Things communications protocol)
Pi has always been a leader in developing new technology and have had a remote access system for over 15 years! The latest iteration of remote access, is called Control InSite and is now a key part of our solution toolbox. Here are some of the features of our remote access:
User interface – A modern and intuitive user interface makes using Control InSite simple. Anyone requiring training can now be trained remotely using remote access and Teams or Zoom.
Speed – The service now runs around 50 times faster than its predecessors, allowing users to connect and download the current sensor values and settings in under 30 seconds (test performed on a CoagSense coagulation controller with 27 different devices such as sensors!).
Reduced data costs – By making the connection between the server and analyser more efficient, Pi has reduced the amount of data required for nearly all tasks thereby significantly reducing costs.
SIM card – By utilising IoT protocols, CRIUS®4.0 remote access can use any data enabled SIM card.
Customer branding – On request, Pi can brand the remote access theme to promote a customer’s brand.
Data analysis – The graphical interface is a powerful and flexible tool for viewing your sensor data. The way we handle your analyser’s data means that every single data point is stored in the cloud, allowing a user to download 3 months’ worth of data with a single click.
Email and text alarms – Direct from the server, cheap and reliable to up to 5 SMS recipients and 5 email recipients.
Data limit – Users can now limit how much data each analyser can use per day, meaning no unexpected data costs.
So what can Control InSite do for you?
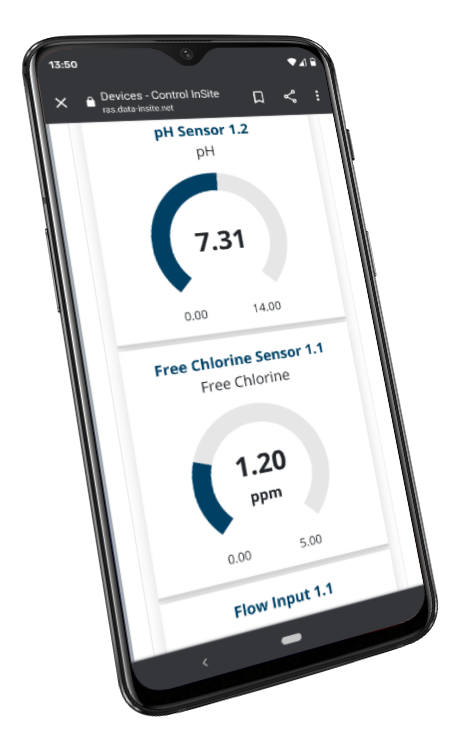
The remote access service has always been designed to save you time and money by allowing you access to the analyser and its data from anywhere in the world. Now remote access can assist as a tool in doing a lot more:
- Remotely checking and changing settings for customers who may not be confident in doing so or who may not have access to the analyser.
- Allowing Pi’s service team to temporarily remotely connect to the analyser if customers have an issue and are unsure about how to solve it.
- Easily view when maintenance is required or due on analysers, allowing users to efficiently plan which sites to visit and when.
- Know when alarms activate on the unit within seconds by enabling text and/or email alerts direct from the analyser.
- Tune control values to optimize dosing without the need to visit the site.
- Analyse stored data to investigate incidents, explain issues or validate the process.
- Save money by reducing the number of callouts and the number of miles your engineers travel!
But what about security?
MQTT is an encrypted ‘internet of things’ communications protocol designed to provide excellent security, so no worries there.
How does user access work?
Each user has their own username and password. This means that what they see and what they can do can be customised so only authorised users can make changes.
Conclusion
Using MQTT means that communication with the CRIUS®4.0 is quick, inexpensive, reliable and secure. The frequency of communication that MQTT allows means that the data you are looking at is effectively live. The size of the packets means that there is no increased data overhead so the costs are effectively the same or lower than other communications protocols that can’t provide live data.
The way the communications works is that the CRIUS®4.0 is in communication to a cloud based ‘broker’. It is then possible for other cloud based services to ‘subscribe’ to the data of that CRIUS®4.0. This means that at the same time the CRIUS®4.0 is talking to Control InSite, it can be talking to a data storage and reporting portal like Data InSite® from Pi or another proprietary portal.
Control InSite is cloud based meaning it is accessible from any internet enabled device anywhere in the world, meaning you can access it without even getting into your car or standing in front of the analyser. This feature is one of the biggest advantages of Control InSite and has been particularly useful during COVID, a time when reducing the number of site visits has been of utmost importance.
You’ve probably heard the phrases ‘Water 4.0’, ‘Industry 4.0’, ‘Internet of Things’ and ‘SMART and DIGITAL’ but did you know that…
…Pi’s CRIUS®4.0 controller was launched with a new remote access platform (the first controller in the world to use MQTT)?
…Pi already has SMART and DIGITAL installations all over the world?
…Pi works as partners to many multinational organisations to provide their remote access, remote comms and SMART technology?
CRIUS®4.0 vs CRIUS® – what’s the difference?
The CRIUS® instrument controller has been upgraded to include the IoT communications package MQTT (Message Queuing Telemetry Transport) and launched in January 2021. All CRIUS® will be CRIUS®4.0 from 1st February 2021 unless by prior arrangement with Pi.
What does MQTT mean to me?
LIVE DATA! MQTT allows very small packets of data to be sent very frequently, which means that when you log on to a CRIUS®4.0 the data you see is updated effectively live. Lots of other things are easier using MQTT. Taking advantage of these means that with CRIUS®4.0…
- Any data-enabled SIM card works with our modems
- Emails and SMS alarms are much cheaper than before
- Much easier to connect to a LAN (Local Area Network)
- Security is enhanced with encrypted data
- The ‘service’ file which details the configuration of the CRIUS®4.0 is readable and downloadable remotely
- Connection to others’ data portals provides REAL TIME, LIVE DATA.
So what is Industry 4.0 (and Water 4.0 and the Internet of Things and SMART and DIGITAL technology)?
Simply put the concept is that we are currently living through the 4th Industrial Revolution.
The first was mechanisation, (what we currently think of as the Industrial Revolution), so steam engines, Spinning Jennies, railways, canals and factories in the 1800s.
The second was the age of mass production so; electricity, the production line, etc., largely in the first half of the 20th century.
The third was computers and automation, in the latter part of the 20th century, and the fourth?
The fourth (Industry 4.0) is about ‘SMART’ factories. (The original use of the expression Industry 4.0 was by a group of advisers to the German government who presented their advice in 2012). Industry 4.0 is about making factories as SMART as they can be. That is having assets (machines, people, robots, AI, cyber technology etc.) all communicating with each other.
The main principles put forward were based on;
- Interoperability – everything should be able to talk to everything else.
- Information Transparency – the physical world should be able to be recreated virtually to allow for testing and modelling.
- Technical Assistance – information should be presented in a way that supports people to make good and fast decisions.
- Decentralisation – after decades of centralisation to things like DCS systems and SCADA systems, the future is to enable as many decisions as possible to be made locally by whatever intelligence (human or machine) is available.
So what is Water 4.0 and SMART and DIGITAL?
Water 4.0 is simply how this technology and philosophy will be implemented/will affect the water industry. There are some clear outcomes from the above… more sensors… more modelling… ‘SMARTER’ instruments, controllers, pumps etc…
SMART and DIGITAL as terms aren’t quite as well defined as others. Generally it is accepted that SMART is the increasing sophistication of equipment to make decentralised decisions. For example, in 1990 a chlorine analyser measured chlorine in water, gave out a 4-20mA output proportional to the chlorine and a couple of relays.
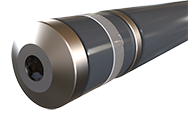
Now the CRIUS® HaloSense (fully Water 4.0 developed) can provide the 4-20mA output and the relays, but also has multiple digital comms options (INTEROPERABILITY), has space for up to 16 sensors (INFORMATION TRANSPARENCY), has wireless and wired internet access (TECHNICAL ASSISTANCE) and full PID capability with remote setpoint, i.e. another device can set the setpoint (DECENTRALISATION). So SMART technology is the technology that allows for the implementation of Industry 4.0 or Water 4.0. DIGITAL tends to refer to the comms capability.
So what is the Internet of Things or IoT?
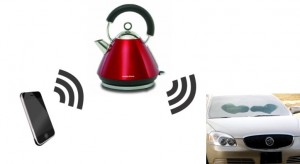
When the previous Industrial Revolutions happened, the technology and concepts spilled over into the consumer world from the business/manufacturing world. With Industry 4.0 it is beginning to be the other way around with consumer demand for the internet, and mobile phone technology, driving the technology. If we assume that in this Industrial Revolution the same thing will happen, then the Internet of Things refers to all devices we use all the time talking to each other and making their own decisions.
Imagine your mobile phone waking you at 6am and telling your kettle that turns itself on at 6.20am, which tells your car that starts itself and defrosts the windscreen at 6.30am etc…
Not convinced that we are in a new Industrial Revolution?
Consider this… perhaps Industrial Revolutions are only identifiable in hindsight?
And what does it matter? Well from Process Instruments’ point of view, it doesn’t. As long as our products are leading the way in providing our customers with what they need to enable their own Industry 4.0, and Pi is leading the way with the world’s first MQTT enabled instrument controller.
Pumps are almost ubiquitous in water processes; whether the pump is the main driver for water flow, is dosing chemicals, or is moving water around a sample line, there is (nearly) always a pump somewhere in the process. Often there are multiple pumps of varying sizes and specifications, making managing all of them a challenge for any operator.
Did you know that…
…today’s leading analysers incorporate the majority of control algorithms a water process should need?
…water quality controllers can often accept fault signals from pumps to help keep your water systems safe and efficient?
…Pi’s CRONOS® and CRIUS®4.0 analysers are the only analysers that can be linked using SMART and DIGITAL communications to a Grundfos DDA pump?
Analysers and controllers will often interact with pumps for a number of different reasons:
- Controlling chemical dosing – controlling a pump to dose a chemical into a system based on one or more measurements (e.g. chlorine residual and flow rate, please see the PID technical note for more information).
- Recirculation control – controlling a pump to manage the recirculation of a system (most commonly used in pools, please see the VSD technical note for more information).
- Failsafe protocols – complex water systems can go wrong for any number of reasons, and analysers can play a role in making those systems safer. Many pumps will output digital alarm signals when they detect a fault, alerting the dosing systems that something needs attention, and to stop dosing the chemical. Dosing into a water system which is not recirculating can lead to dangerous overdosing, and also wastes chemicals leading to increased costs.
- Duty rotation, or n+11 back-ups – in larger systems, pumps may be rotated in order to increase pump longevity or have a back-up system to rely on in the case of pump failure. Having a back-up, or n+1 system, can often reduce downtime significantly, and so is very useful in production lines where downtime can lead to large cost increases.
1n+1 is a standard term used when considering redundancy. The ‘n’ indicates the number of items required to run the systems so, in this case, the number of pumps. The ‘+1’ indicates the number of back-up systems in place.
Here is a summary of the different kinds of signals that can be used to interact with pumps, some of the common applications they are used in, and their advantages and disadvantages.
Power switching relay based control
Description: Power On/Off provides power to pumps when the analyser needs the pump to be on, this can be 12-230V. Pumps are off and have no power when they are not pumping.
Advantages: Cheapest and most universal method of control.
Disadvantages: High pump and relay wear.
Commonly used for: Small dosing pumps, pools, small water systems.
Volt Free Contact (VFC) Control
Description: The pump is powered separately to the analyser, and only begins to pump when a low voltage control circuit is closed. VFC can be used with thresholds or with PID and can be used as on/off control or pulse width/frequency.
This means that the analyser can mimic a flow meter’s ‘Pulse Control’.
Advantages: Very commonly accepted by pumps and protects both the relay and the pump from high voltage surges.
Disadvantages: Not as precise as analogue control, especially for non-recirculating systems.
Commonly used for: Small to medium dosing pumps, pools.
Analogue Control
Description: Either a 4-20mA or 0-10V is scaled to match the pump output, and then is used to control the pump rate.
Advantages: Very precise control, even on non-recirculating systems. The pump is on all the time eliminating power surges and start-up fatigue.
Disadvantages: Can only be used on pumps that accept analogue inputs.
Commonly used for: Medium to large systems, large pool systems, any system where precise dosing is a necessity.
SMART and DIGITAL control
Description: Some pumps can now be controlled using digital communications such as Modbus or Profibus. These are designed to be used directly from PLCs and they give operators distinct advantages over more traditional methods. A digital signal has longer range, has a signal cable for 2-way communication, and is able to transmit far more detailed information than a simple on/off alarm signal.
An example of a pump with SMART and DIGITAL communication is the Grundfos DDA dosing pump with e-box add-on. The e-box provides a Modbus or Profibus connection for 2-way communication.
The CRIUS®4.0 instrument controller from Pi is the only water quality analyser capable of utilising the full range of information available from the DDA pump. Information such as: total pump run time, pump pressures, volume pumped, and many more are now available to the analyser.
Error alerts can now be specific, telling operators exactly what needs to be done with their pump. This wealth of information can be useful in co-ordinating maintenance and increasing uptime for the pump and the system as a whole. All of this information can be stored, and data-logged, making the system very auditable.
Normally all of this information would only be available to operators with access to a PLC, and a PLC engineer able to integrate the two systems, but the CRIUS®4.0 from Pi is a customisable controller that doesn’t need a PLC engineer to configure.Control with the DDA e-box can also be extremely precise, with the pump more able to correct the pump output to very closely match the scale used by the analyser. A pump being controlled by a 4-20mA scale, asking for 60% of the pump’s output, was more than a litre off the real value of 60% of the pump’s scale. This means that on a 0-30l/h pump, a pump controlled by a 4-20mA signal calling for 60% of the pump’s output would actually be pumping 19l/h, whereas a Modbus controlled pump would be pumping 18l/h. This difference is small but measurable, and over a pump’s lifetime would add up to a remarkable discrepancy in chemical. It’s likely that with longer cable lengths, on a real site, this discrepancy would increase.
Advantages: The most precise control, excellent maintenance information, more uptime for processes.
Disadvantages: Currently only available with Grundfos DDA pumps and Pi analysers.
Commonly used for: Large to very large systems, or 24hr systems where savings on chemicals and reduced downtime are amplified. Food systems in particular benefit from increased uptime and excellent auditability.
There are many ways for analysers to interact with pumps, and no single way is a ‘one size fits all’ solution. Whether you are retrofitting to an existing system, or designing a new plant with the latest in SMART and DIGITAL communications, Pi’s instrument controllers have you covered.
Process Instruments supply CRIUS®4.0 and CRONOS® controllers with sensors for many single parameter systems like chlorine and pH but did you know that…
…Pi’s CRIUS®4.0 and CRONOS® controllers both allow the connection of multiple sensors?
…Pi’s multi-parameter systems can save you space onsite, are easy to use and have a number of communications options available?
…Pi’s CoagSense coagulation controller is a multi-parameter system that is now a key part of Pi’s product range?
An example of one of Pi’s most in demand multi-parameter analyser combines a CRIUS®4.0 with a TurbSense® turbidity meter, a pHSense pH meter, a ConductiSense conductivity meter and a UV254Sense UVA analyser with a temperature sensor on raw water systems. These have proven to be very popular in applications where companies and local authorities are looking to save on installation time, space and upfront costs.
Pi’s Multi-Parameter Controllers
Pi’s CRIUS®4.0 Controller
The CRIUS®4.0 is equipped with the capability to connect up to four sensors of any type with appropriate analogue outputs and relays. If four isn’t enough, don’t worry. The CRIUS®4.0 can connect up to sixteen sensors by adding expansion boxes where needed, all using the same display and communications.
Equipped with data logging as standard and multiple PID loops as options, the CRIUS®4.0 is a cost effective alternative to multiple single sensor analysers, reducing cost while maintaining the highest quality.
Optional communications packages allow Profibus, Modbus ASCII, Modbus RTU, Modbus TCP, 4-20mA analogue outputs, and relays for alarms and control.
Customers requiring a no-frills controller should consider the CRONOS® controller.
Pi’s CRONOS® Controller
The CRONOS® has the capability to control up to two sensors of any type with appropriate analogue outputs and relays. Equipped with optional PID control, the CRONOS® is very able to control complex water treatment processes at a fraction of the cost of other controllers.
Advantages of Pi’s Multi-Parameter Systems
1. Space Saving
Finding space is becoming a real problem for installation engineers across many sites at the moment. As water supply companies are looking for more and more information and regulation increases, this has resulted in more and more instrumentation being installed. Most water treatment plants have limited wall space and finding room for new instruments is a real challenge. Both of Pi’s instrument controllers as multi-parameter analysers are solutions to this problem.
2. Easier to Use
With simple ‘plug & play’ inputs and outputs, intuitive display and button control, and with an individual manual configured to be the same as your analyser, the CRIUS®4.0 and CRONOS® make setup and ongoing use, simple and easy.
3. Communications
Modbus and Profibus communications are available which further cut down on wiring costs and PLC, SCADA input costs.
4. Remote Access
Pi’s remote access allows the user to connect their CRIUS®4.0 through their local network (LAN) or a 3G/4G mobile network connection. This connection allows the user to have full control of their analyser from any computer, tablet or mobile phone.
CoagSense Coagulation Controller
The CoagSense coagulation controller combines a StreamerSense streaming current sensor, a UV254Sense UV analyser and a pHSense pH sensor to automatically control pH adjustment of the raw water and also the coagulant dosing in water treatment plants. A TurbSense® turbidity meter can also be added if required.
The controller has revolutionised the industry where one controller can now monitor and automatically control your dosing pumps by sending a flow proportional signal direct to the dosing pumps, or to the plant’s SCADA. Previously, all of this had to be done by a PLC or a SCADA system which involved getting a specialist programmer on site and increased costs. Now there is a controller that does all of this in an affordable manner.
Process Instruments (Pi) are increasingly seeing water engineers and technicians relying on their PLC’s PID auto-tune feature. Many are becoming frustrated that the auto-tuners are unreliable when it comes to water processes. Sometimes the auto-tuned PID settings work, but then something changes in the process and the PID control no longer functions correctly.
In this Focus On, Pi aims to outline how PID auto-tuners work and why they are often unsuitable for complex water treatment processes. We also give a brief introduction to some of the principles of tuning a PID manually.
Did you know that…
…auto-tuners are not effective at tuning processes with long loop times?
…the CRONOS® and CRIUS®4.0 have many built-in PID safety features to make control easier and safer?
…PID loops can often be tuned remotely, meaning huge savings on site visits and travel time?
What is PID tuning?
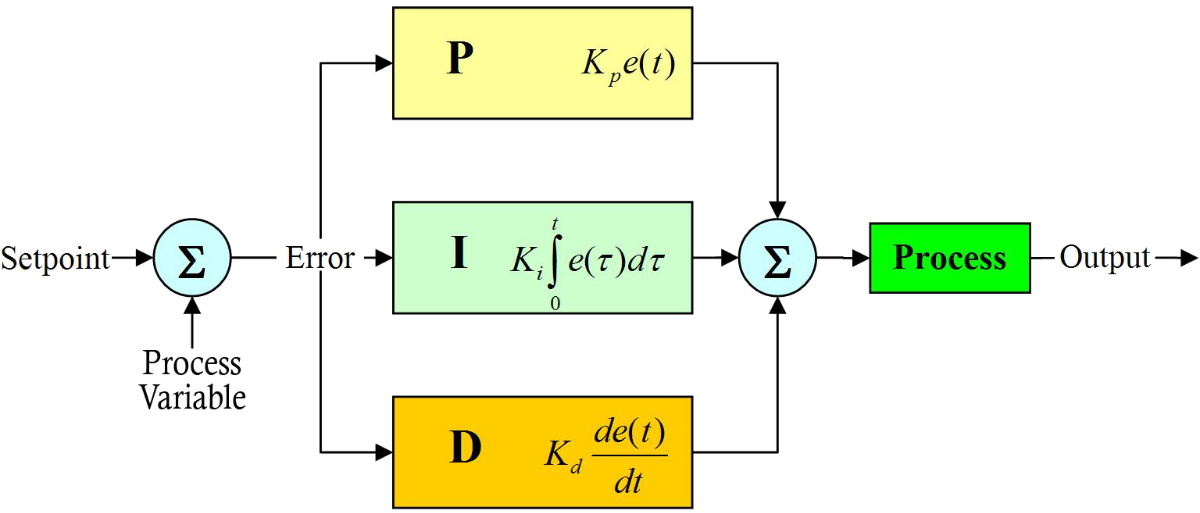
A Proportional – Integral – Derivative (PID) controller is a control loop feedback mechanism widely used in industrial control systems. PID controllers allow a system to continuously and automatically modulate a control mechanism (e.g. a dosing pump, a valve, motor speed), to attempt to achieve a desired setpoint.
There are a myriad of ways that a PID controller can be ‘tuned’. In a very basic PID controller, the operator can choose how much of their control should be based on P, I and D. In reality, D is almost never required in water processes due to the nature of the control loop.
This is generally what ‘auto-tuners’ undertake. They make small changes to the ratio between P, I and D control, track the response, decide if the change is good or bad, and then change again.
What is the auto-tune doing?
So what the auto-tuner is doing is changing, measuring, and changing again; which can work perfectly on processes with a very short loop time (time between a change and a response from the system), the auto-tune making many changes in a short amount of time. The changes cumulate into a ‘tuned’ PID system.
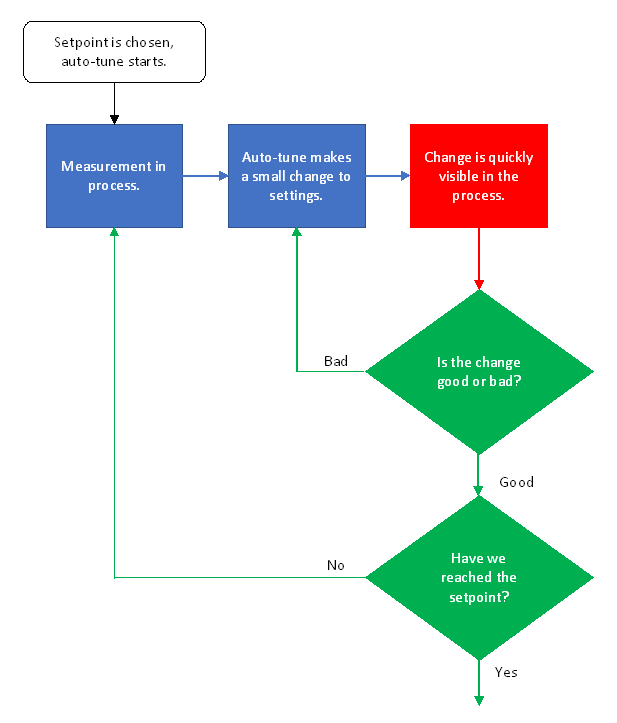
On the right is an example system of a PID auto-tune.
In the diagram, we can see that for the system to work, the box in red is a crucial part of the process. If the change brought on by the PID auto-tuner isn’t visible quickly enough, it may affect the way the auto-tuner categorises the change (good or bad), or won’t give the auto-tune the opportunity to make enough iterative changes to bring a complex water system under control.
The good news
There is good news for water technicians and engineers and that is that Pi are here to help. All our salespeople are application specialists and are all capable of helping you manually tune a PID controller for your processes. Our CRONOS® and CRIUS®4.0 controllers are both capable of delivering excellent control in many processes, and have many built-in PID features to help make your process more controlled, robust and safe.
Where to start with PID tuning
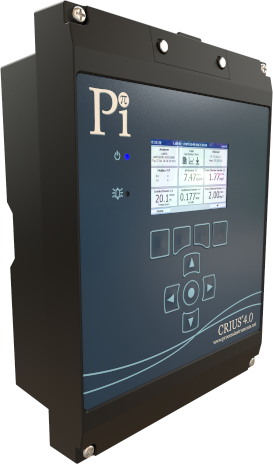
In many ways, the auto-tuners mimic plant engineers making adjustments and tuning their PID settings. They simply lack 2 key components;
- Patience – because the loop times are so long, it will take time to tune a PID loop.
- Context – no auto-tuner can account for blocked dosing lines, or 2 identical pumps that are improperly calibrated and output different volumes, or seasonal changes in measured parameter concentrations. Context is incredibly important in tuning a PID loop.
With this in mind, here is how our engineers approach PID tuning on our instruments;
- Check the measurement and output method are all working properly. This includes any calibration on the probes and on the pumps as well as checking that the dosing lines are clear.
- Consider the loop time and change the PID’s Update Delay. This changes how often the PID algorithm makes a change to the output.
- Start small and ramp up. Start with the P control and slowly increase the P factor until it is changing the measurement in a satisfactory timeframe. If you can get a good level of control with just P then that’s excellent. There is often no need to overcomplicate things past this. The addition of I and D components is often unnecessary.
- If you have wild or erratic control lower the P until the control is stable, even if it doesn’t reach your setpoint then add some I control.
- Always aim to have I as low as you can get away with, as I can cause more problems with control than it solves.
Once you have the basic P and I ratio sorted, or if you are unable to get the P and I into control, it is worth considering these additional settings which will help make your control scheme more robust and safer.
- Min/Max Output – restricts the range that the PID can work within, which can stop potential over- and under-dosing. This setting may also reduce the ability of the PID loop to respond to changes in the water.
- Start Mode – allows the process to be dosed using a flow proportional value or a manual percentage value, during a predetermined start up period. This is often used to get the process up and running before going into PID control.
- Ramping – smooths the start-up of the process where the error between the measured value and setpoint may be very large (which can cause erratic overshoot and overcorrection).
- Bumpless Transfer – smooths out the process of switching between manual and automatic control.
- Integral Wind Up Protection – puts a limit on the effect of I because I looks at error over time. A very small error over a large amount of time can result in a very large I output resulting in erratic control.
- Overfeed Protection – protects against the failure of other equipment, such as failing pumps or blocked dosing lines. This puts the control into alarm if the controller is calling for dosing but is seeing no change.
How our products can help
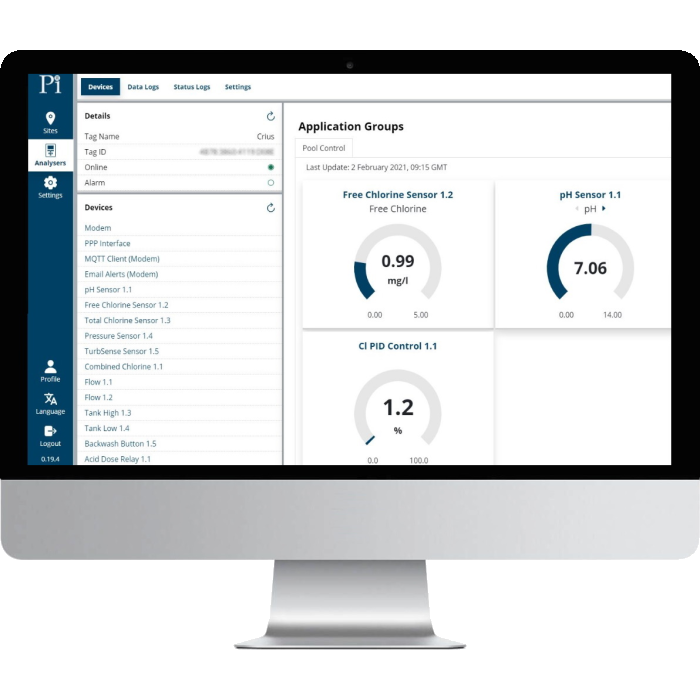
Even armed with all this knowledge, PID tuning can be a bit of a dark art. What works on one site may not work on another and even experienced engineers sometimes call us for help.
One of the ways we can help is using our remote access system InSite. Our Remote Access portal (Control InSite) allows people with the appropriate security clearance to make changes to settings and observe measurements from their desk.
Sales Manager, Dr. Rob Paramore, recently described his experience of changing a customer’s PID settings (at their request), whilst talking them through what he was doing on the phone:
A VSD is an electronic device which enables a pump motor to be turned up or down thereby increasing or lowering the pump speed. Most pool recirculating pumps are over specified for the duty required and as such, there is scope using VSDs to turn them down when possible and save considerable amounts of money on electricity costs.
Did you know that…
…VSD control has saved some swimming pools more than 35% on their electricity bills?
…Pi’s VSD control saves money during the night and even during the day when electricity tariffs are highest?
…VSD control is available on both Pi’s CRONOS® and CRIUS®4.0 controllers?
What is the problem?
High electricity bills and high CO2 footprint.
Most swimming pools and spas spend considerable amounts of money on electricity to run their pool water recirculation pumps. These pumps are often over specified, running at full power even when there are few or no bathers using the pool or spa during the daytime. With recirculation pumps continually running at full power, the monthly electricity bills can be very high. A result of this high electricity demand is an increased carbon footprint of the pool or spa. Current VSD controls only lower the pump speeds to reduce the pool or spa’s water recirculation to a minimum overnight when there are no bathers.
What is the solution?
Process Instruments’ CRONOS® and CRIUS®4.0 Controllers with VSD
What is required is a VSD control which in addition to reducing power consumption overnight can also save costs during the day by turning the pumps down when there are few bathers.
Pi’s controllers have the capability to utilise VSD control during the day and at night; swimming pools and spas can benefit from turning the pumps down even during the day when electricity costs are highest.
How does VSD control work?
Pi’s VSD control sets the recirculation pump motor automatically, while the pool is being used, based on biocide demand. Biocide demand is directly linked to the number of people using the pool or spa, therefore Pi’s controllers can reduce pump speeds and electricity costs during periods of fewer bathers.
The graph shows how VSD control works, based on biocide demand. Looking at the graph, thresholds are set at different levels of biocide. These thresholds are then used to create biocide level bands, with each band being attributed with a specific pump speed. This optimises water recirculation whilst maintaining the minimum turnover (number of times the pool’s water recirculates in a given time) set by the manufacturer or consultant at the time of installation. During daytime periods when the number of pool users fluctuates, the bather load increases/decreases respectively. As the biocide demand is directly proportional to the bather load, fewer users will result in biocide levels dropping below the band threshold thus enabling a reduced pump speed during the day. Pi’s VSD control exploits this relationship between biocide demand and bather load adjusting the pumps speeds during the day hence saving the pool or spa money on electricity.
In addition to pools and spas saving money on their electricity, they are effectively reducing CO2 emissions and the carbon footprint of their establishment. For many organisations, reducing CO2 emissions is a significant factor in choosing which equipment to purchase.
Swimming Pool Application Savings Data
For a commercial swimming pool (210m3) the monthly savings on electricity using VSD control were calculated.
The power consumption of the recirculation pump was recorded for a month with Pi’s VSD control enabled and without VSD for the same period. Using standard day and night electricity tariffs, it was possible to calculate how much money can be saved by using VSD control.
Over a period of a month, energy costs were calculated.From these results it can be seen that Pi’s VSD control saved £213 a month at this single commercial swimming pool. This is a significant reduction not only in cost but also the CO2 footprint of the site. The larger the pool and spa, the bigger the pump that is required to recirculate, therefore the more money that can be saved on electricity. Using the VSD control; Pi’s controllers could pay for themselves in 6 months or less.
If you have used a Pi controller you will know that they give you unrivaled control options but did you know that…
…Pi’s controllers also offer individual security for up to 20 named individuals?
…Pi’s controllers have always given flexibility but now Pi’s controllers can accommodate up to 16 sensors of any description?
This Focus On describes the 10 most popular innovations to be found in Pi’s CRONOS® and CRIUS®4.0.
No. 1 – Human readable service log
Both the CRONOS® and CRIUS®4.0 analyser/controller has a downloadable human readable service log – giving an entire history of the instrument including current settings, calibrations etc., providing a great snapshot of how an engineer left an instrument.
No. 2 – Cloning facility
Ever had to set up many instruments with the same settings? Simply set up one and copy it to others!
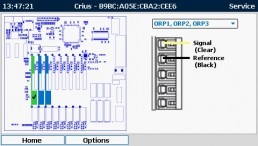
No. 3 – On screen wiring diagrams
Lost the manual or can’t be bothered to find it? Pi’s analysers have the answer!
No. 4 – Want a bit more info on what’s going on with a sensor?
Pi’s new sensor maintenance pages are just for you then! Detailed information about all aspects of the signal coming off the sensor clearly available.
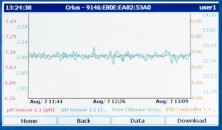
No. 5 – Instrument data logs not quite giving you what you need?
Pi’s new look data logs in CRONOS® and CRIUS®4.0 (downloadable) let you data log almost everything, put graphs on the display, data log the same parameters at more than one interval and a whole lot more. Never has instrument data logging been so easy and complete.
No. 6 – Enclosure
The enclosure brings a new level of flexibility being wall mountable, pole and handrail mountable and even flush mountable. Not only that, but it gives you loads of room to work in and there are even spare live, neutral and earth terminals to make wiring relays easier!
No. 7 – Not enough I/O?
Don’t worry, simply daisy chain 4 CRIUS®4.0 together and you can use the same display, comms options etc. and increase your I/O fourfold to give up to 16 sensors.
No. 8 – Bored of reading about stuff in manuals that you don’t have?
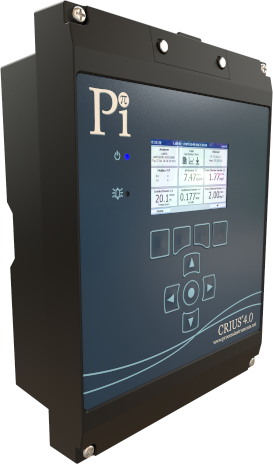
Pi’s manuals are bespoke to each instrument. The manual is ‘built’ to match each individual instrument so the manual only has what you have!
No. 9 – Has the operator been messing with settings they shouldn’t?
No more! With 20 individual user settable logons, you can give people access to what they need and no more.
No. 10 – Control algorithms
Pi has developed a reputation for developing great control algorithms and this has continued with the new CRONOS® and CRIUS®4.0 with the introduction of feed forward control algorithms and a master controller which selects the correct control philosophy to use (for use with complex systems such as coagulation control).
Did you know that…
…PID can save you money by offering better process control?
…PID can help you maintain a setpoint, even with a variable process?
…the days of over complex and confusing PID are over?
…Pi can tailor a PID system to your exact requirements? You may never have to touch those settings again!
In this Focus On, Pi would like to introduce you to PID if you haven’t come across it, and discuss some of the useful advanced features of modern PID systems, like on Pi’s CRONOS® and CRIUS® models for those more familiar with PID.
What is PID?
PID is a mathematical tool created by engineers and is used in controllers. It is a feature often found in industrial controllers and is available in Pi’s controllers, as an inexpensive upgrade.
What is PID for?
The best way to explain what PID does, is to take an example. Most people have been to a swimming pool at some point in their lives, so this is the example we shall use. PID is also applicable in a huge variety of other processes. If you are not sure, you can always contact us to discuss your application.
When a person enters a swimming pool, they create a chlorine demand. They do this by introducing sweat, bacteria, organic molecules and other substances into the pool water. Chlorine reacts with these substances, which results in chlorine being used up and the chlorine level dropping. The chlorine level in this example, is often called the process variable or PV in the context of PID.
In order to maintain a concentration or level of chlorine, more chlorine needs to be dosed. If you dosed the same amount of chlorine per bather, the level would not be stable as all bathers create a different chlorine demand (e.g. swimming for fitness produces more sweat than swimming recreationally). Dosing manually brings in the issue of human error, and how operators approximate or calculate the amount of chlorine to dose based on current levels. Another issue with manual dosing is that it is not a continuous process, meaning it is unlikely a stable level will ever be reached.
What does PID do?
PID takes the measured level of chlorine or the PV and compares it to the desired level or set-point. This comparison gives the error which PID interprets and then calculates an output. The output is an electrical signal which controls the dosing of the appropriate chemical. The output can control heaters, dosing pumps and many other mechanisms that can be used to change the PV.
How is it used?
PID is made up of three parts, proportional, integral and derivative. Understanding what each part does helps operators choose the level of control best suited to them.
Proportional – Is the most commonly used for portion PID and suits most applications. When using proportional control, the further away the measured value is from the setpoint, the larger the output will be from the controller. This is an appropriate level of control for most processes, and users can gain a lot of control from a purely proportional system.
In some systems where the PV is lost to the process, e.g. chlorine from a pool, heat from a boiler etc., the proportional control never quite catches up with the setpoint. Users can see that although the process approaches the setpoint it rarely, if ever, gets to it. This is known as ‘droop’. The user can compensate for droop if the removal of the PV is fairly constant, simply by raising the setpoint, e.g. evaporation of chlorine from an empty pool. If droop changes often, (e.g. bather load or chlorine demand) then to eradicate the ‘droop’ then the integral part of PID can be applied to the signal to correct it.Integral – The output from the integral term is determined by both the magnitude and the duration of the error. A small error over a long period of time will trigger a larger response than from a purely proportional system. This helps the elimination of the ‘droop’ seen in processes with continuous loss, and also serves to help reach the setpoint quicker.
Derivative – Derivative gain is rarely used and is generally set up only by expert engineers. Derivative gain uses the rate of change in the PV to try to predict future errors. This type of control is particularly susceptible to overcompensating, especially if there is even a small amount of signal noise (usually seen as spikes in the PV). Derivative gain is generally a tweak used by engineers to improve an already tight control, and is almost never used as an essential part of control.
What are the benefits of PID?
When properly set up, PID can lead to far tighter process control, which in turn can save you time and money. As an example, pool managers want to keep chlorine levels low, to improve the bathing experience and also save on chemicals. AquaSense is a chlorine analyser system that responds quickly and appropriately to a change in bather load (also known as chlorine demand). This means pool operators can save money whilst maintaining the safety of the pool. PID can also help reduce the risk of overshooting the desired setpoint, reducing the risk of dangerous overdosing of the chemicals.
Advanced Features and Safeguards
Whilst maintaining a setpoint with a PID loop is a huge advance over using threshold relays to maintain an upper and lower limit, it is sensible to control the loop with extra safeguards, such as:
- Maximum and minimum pump outputs. This is mainly used to prevent the controller from employing too aggressive a control, which can lead to overdosing. A minimum output can also be used in a system where the measured parameter is lost over time, to prevent the controller ever turning the dosing off.
- Ramp rate is a proportional control that allows users to choose how quickly or slowly the controller doses, in order to reach the setpoint. It is especially useful on startup, and can prevent the controller dosing too quickly.
- Wind up protection is an integral control, which limits the duration aspect of the control. This puts a limit on how much previous error can accumulate. Without wind up protection, there could be a very large integral value, if the process ever reaches zero or on startup.
These are all standard features in all Pi PID controllers.
Conclusion
In summary, PID is a very useful tool when used correctly, and can result in significant chemical savings, not to mention reduced pump wear and tear and lower electricity costs.
Document | Type | Size |
---|---|---|
CRONOS® | Brochure | 656kB |
CRIUS®4.0 | Brochure | 860kB |
How To Specify a Pi Analyser | Technical Note | 815kB |
Water 4.0, Industry 4.0, IoT, SMART and DIGITAL | Technical Note | 727kB |
CRONOS® and CRIUS®4.0 Control Options | Technical Note | 608kB |
Remote Access – InSite | Brochure | 1.3mB |
Remote Access – LIVE DATA | Technical Note | 586kB |
PID Control | Technical Note | 710kB |
VSD Control to Reduce Swimming Pool Electricity Bills | Technical Note | 665kB |
"The support from Pi and its partners is superb. They go above and beyond to ensure that, not only is their equipment perfect but that the process is working great too. Five Stars!"
Anthony Glitto
Equip Solutions - Illinois, USA
Everyone at Pi goes out of their way to be supportive and timely. Their expertise is unchallenged and I am very happy to endorse them as a quality supplier.
John Clark
Chemtrac - Georgia, USA
Servicing customers is much more than just solving problems or addressing complaints and Pi does that very competently with technical and quick efforts providing a good experience.
Clovis Tuchapski
Buckman - Latin America